
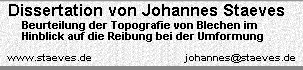





6.2 Auswahl der Ausführung der Anlage
Größe und Lagerung der Werkzeuge
Zur Beurteilung der Topografien wird im Rahmen dieser Arbeit die am
Institut des Autors vorhandene Reibversuchsanlage gewählt. Als Vorteil
erweist sich bei dieser Anlage neben dem Prinzip vor allem die Größe
der Werkzeuge. Die maximale Werkzeuglänge beträgt 144 mm, die
Breite 74 mm. Wenn die Wirkung der Quetschströmung beurteilt werden
soll, dann sind, wie im Bereich unter dem Niederhalter eines Realwerkzeugs,
größere Flächen erforderlich (Bilder 21 und 23). Zur Beurteilung
der Topografien wird deshalb die volle Werkzeuggröße genutzt.
Bei der Werkzeuggröße von 144 x 74 mm² werden je nach Schmierstoff,
Topografie und Geschwindigkeit maximale Kontaktnormalspannungen bis ca.
20 N/mm² erreicht. Diese Werte liegen, wie auch die FE-Simulation
des Pedaltopfs zeigt [77], deutlich unter den maximalen Flächenpressungen
in realen Werkzeugen. Bei Verwendung kürzerer Werkzeuge lassen sich
im Streifenziehversuch auch die hohen Werte der lokalen Kontaktnormalspannungen
abbilden. Die Ergebnisse in Kapitel 6.1 zeigen aber, daß nicht die
kleinen Bereiche mit den hohen Kontaktnormalspannungen in der Matrizenrundung
(Umlenkversuch), sondern die größeren Flächen im Niederhalterbereich
mit den moderaten Kontaktnormalspannungen (Flachbahnversuch) den entscheidenden
Beitrag zur Reibung liefern.
Die Werkzeuge sind horizontal in Linearlagern geführt und stützen
sich auf Wägezellen ab. Das Verkippen der Werkzeuge wird durch
die steife Lagerung und das Abstützen der Reibungskraft in Blechebene
verhindert. Infolge der Länge der Werkzeuge von 144 mm wirken die
in Kapitel 5.2.6 beschriebenen selbstausrichtenden Effekte.
Reinigung des Bleches
Das Blechmaterial wird direkt vom Coil verarbeitet. Durch die kontinuierliche
Betriebsweise ist es möglich, eine hohe Versuchszahl mit entsprechender
statistischer Absicherung durchzuführen. Das Blechmaterial ist üblicherweise
mit einem im Walzwerk aufgebrachten Korrosionsschutzöl versehen. In
der kombinierten Reinigungs- und Beölungsanlage wird zunächst
das Korrosionsschutzöl entfernt. Dazu wurde eine modulare Reinigungs-
und Beölungsanlage entwickelt, die es durch unterschiedliche Modulauswahl
und -anordnung ermöglicht, unterschiedliche Reinigungsverfahren einzusetzen.
Ausgehend von bereits veröffentlichten Ergebnissen des Autors [77]
wird für die Untersuchung der Topografien die Hochdruckreinigung mit
niedrigviskosem Öl gewählt. Anschließend trocknen zusätzliche
Module das Blech mit zwei Abquetschwalzenpaaren, einer Rakel und einem
Druckluftvorhang.
Beölung des Bleches
Für die Beölung wird ein Modul verwendet, das den Schmierstoff
über Kalanderwalzen auf das Blech überträgt. Bei diesem
Verfahren ist die Schmierstoffmenge über den pneumatisch einstellbaren
Anpreßdruck der Walzen regulierbar.
Um die richtige Applikationstemperatur des Schmierstoffs sicherzustellen
und Ablagerungen am Behälterboden zu vermeiden, wird der Schmierstoff
ständig umgewälzt und auf einer konstanten Temperatur von ca.
38°C gehalten.
Die Reinigungs- und Beölungsanlage fördert das Blechmaterial
mit konstanter Geschwindigkeit, um einen homogenen Schmierfilm sicherzustellen.
Die lichtschrankenüberwachte Schlaufengrube dient als Blechspeicher.

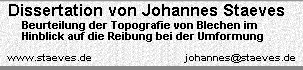




